Individuelle Druckfeder für Serienprodukt: kleine Anpassung mit großer Wirkung
Industrielle Federn sind mehr als nur Standardbauteile – sie müssen exakt auf den Anwendungsfall abgestimmt sein. Faktoren wie Einbauraum, Belastung, Anforderungen an die Lebensdauer und Montagebedingungen erfordern häufig individuelle Lösungen.
Die folgende Fallstudie zeigt, wie eine präzise ausgelegte Druckfeder aus einem austenitischen Chrom-Nickel-Stahl nicht nur den grundsätzlichen Anforderungen entspricht, sondern durch eine gezielte Anpassung auch die Serienmontage deutlich vereinfacht.
Herausforderung aus der Industrie: Rückstellbewegung in Baugruppe
Ein Industriekunde plante in einer Baugruppe die Realisierung einer definierten Rückstellbewegung durch eine Druckfeder. Die technischen Rahmenbedingungen waren klar vorgegeben: ein begrenzter Einbauraum, konkrete Bauteilgewichte sowie die Anforderung einer sehr hohen Lebensdauer – 10 Millionen Zyklen sollten dauerhaft erreicht werden.
Auf Basis dieser Parameter entschieden wir uns für eine individuell ausgelegte, dauerfeste Druckfeder aus dem Werkstoff 1.4310. Dieser austenitische Chrom-Nickel-Stahl zeichnet sich durch hohe Korrosionsbeständigkeit, gute Umformbarkeit und hervorragende mechanische Eigenschaften aus – ideal für dynamisch beanspruchte Federn mit hoher Zyklenzahl.
Technische Lösung: Auslegung und Prototypenprüfung
Nach der Berechnung der Feder entsprechend der kundenspezifischen Vorgaben wurden erste Prototypen gefertigt. Die anschließenden Dauertests bei unserem Kunden verliefen erfolgreich: Die Feder erfüllte sämtliche Belastungskriterien und zeigte keine Ermüdungserscheinungen.
In der praktischen Anwendung in der Serienproduktion trat jedoch ein unerwarteter Nebeneffekt auf: Die Feder war bei der Montage schwer zu handhaben, da sie während des Einbaus nicht im Federsitz fixiert blieb und leicht herausfiel. Dies führte zu erhöhtem Aufwand und einer potenziellen Fehlerquelle in der Produktion.
Optimierung für die Montage: Anpassung der letzten Federwindung
Gemeinsam mit dem Kunden analysierten wir die Montagesituation und erhielten das betroffene Bauteil zur Bewertung. Durch eine gezielte Vergrößerung der letzten Federwindung wurde erreicht, dass die Feder nun im Federsitz klemmt. Diese konstruktive Anpassung verbessert die Positionierung und Handhabung während der Montage erheblich, ohne die ursprüngliche Funktionalität und Lebensdauer zu beeinträchtigen.
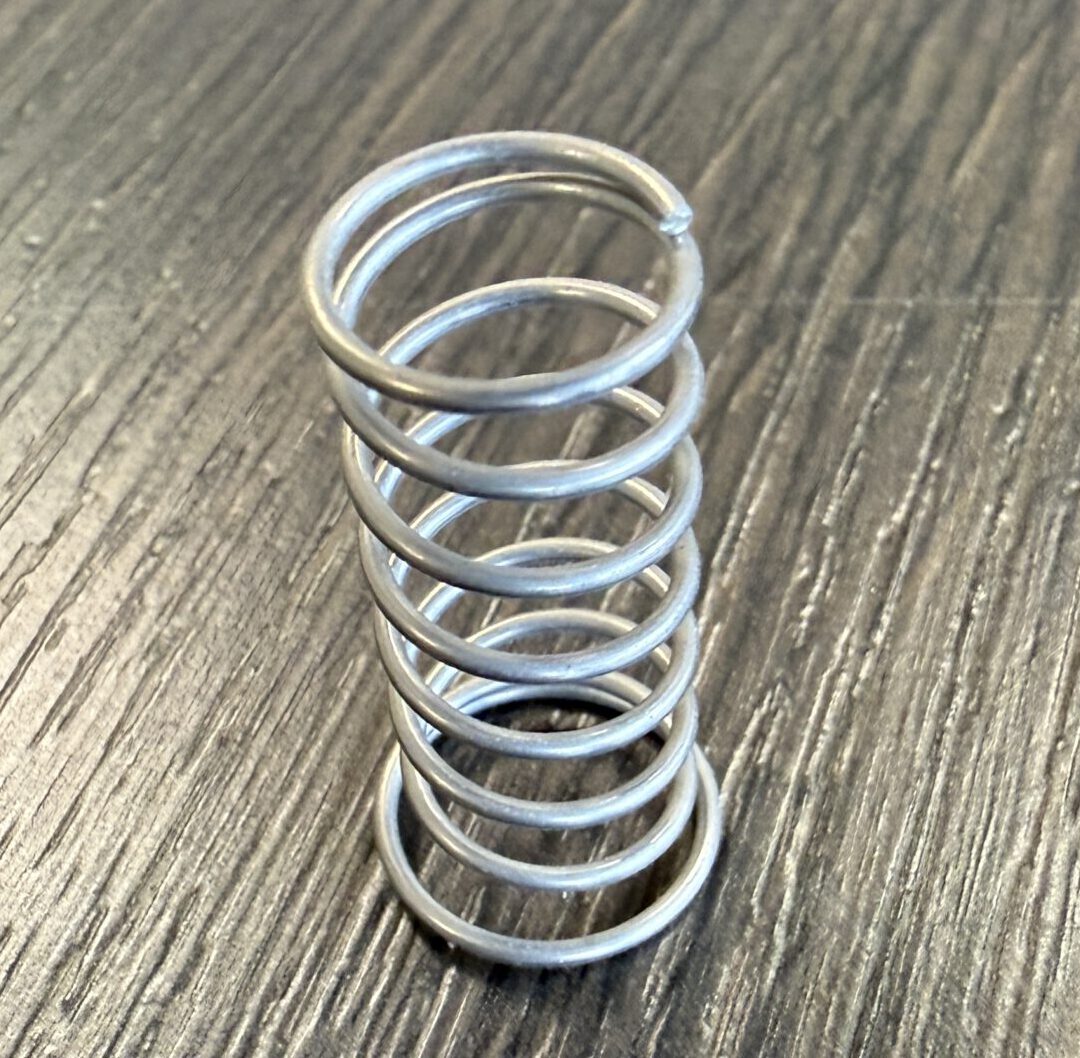
Der Vorteil: eine deutlich einfachere Montage, weniger Aufwand im Produktionsprozess und eine Reduktion potenzieller Fehler in der Montage.
Fazit: Individuelle Federlösungen bieten technischen und praktischen Mehrwert
Dieses Beispiel verdeutlicht, wie kundenspezifische Federlösungen nicht nur funktionale Anforderungen erfüllen, sondern auch Verbesserungen im Montageprozess ermöglichen. Durch die Kombination aus präziser Auslegung, passendem Werkstoff und konstruktiver Optimierung konnte eine Lösung realisiert werden, die sowohl die technische Belastbarkeit als auch die Alltagstauglichkeit in der Serienmontage sicherstellt.
Ihre Anwendung – unsere Lösung
Sie planen ebenfalls ein Projekt, bei dem Standardfedern nicht ausreichen? Bei Achenbach Federn unterstützen wir Sie bei der Entwicklung individueller Federn für anspruchsvolle industrielle Anwendungen – von der Berechnung über die Prototypenfertigung bis hin zur Serienreife.
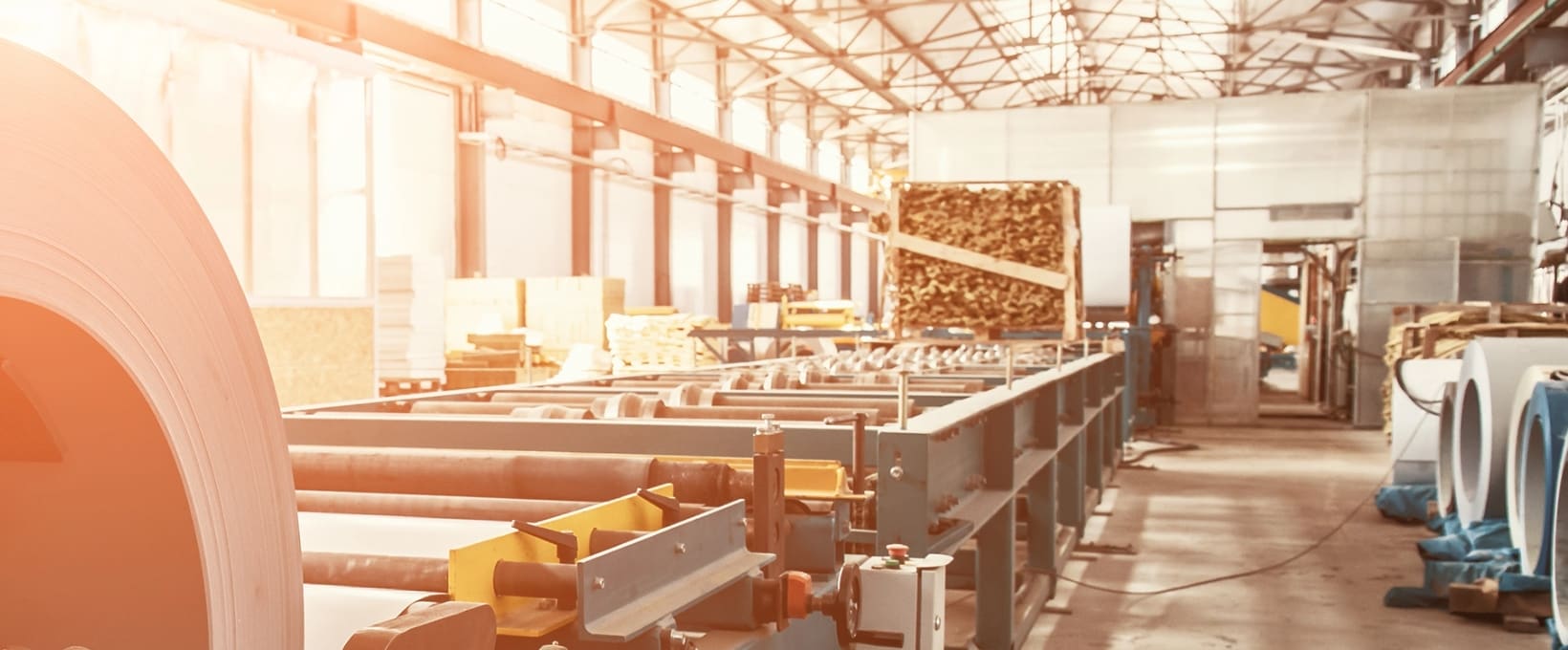